I have a couple of stepper motors that I can use that were taken from an old plotter that was found in a skip, they are both rated at 24V
but I intend to run from the same 15V supply as the Rubidium frequency source. Both motors have 48 steps per revolution so they would need to be geared at
1.25:1 to get 60 steps per turn
The Microchip application note AN907 gives a stepping sequence for a unipolar motor as shown below:
That table can be rearranged as shown below:
1A |
2A |
1B |
2B |
1 |
0 |
0 |
0 |
0 |
1 |
0 |
0 |
0 |
0 |
1 |
0 |
0 |
0 |
0 |
1 |
1 |
0 |
0 |
0 |
0 |
1 |
0 |
0 |
0 |
0 |
1 |
0 |
0 |
0 |
0 |
1 |
1 |
0 |
0 |
0 |
0 |
1 |
0 |
0 |
0 |
0 |
1 |
0 |
0 |
0 |
0 |
1 |
So this stepping sequence can be implemented as a very simple bit shift using half an 8-bit port. This is actually something that I've done before,
a few years ago I designed my own ECU for my Suzuki Vitara, the code was lost years ago but I dug out the PICDEM2 based hardware and wrote some new code
for it, it was up and running in quite a short time so the next step (pun intended) was to test the plotter motors.
The HP plotter motors
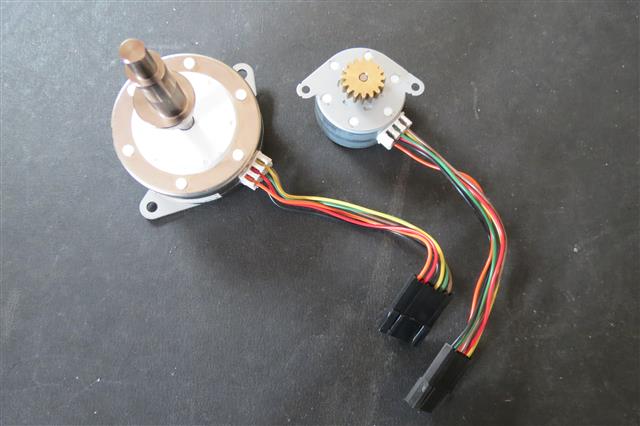
     
Both motors use the same wire colours but not the same pinout! using the same nomenclature as the Suzuki Stepper Motor EGR the pinouts are as shown below:
PM55L-048-HPB7 |
PM35L-048-HPF7 |
Pin |
Colour |
Pin |
Colour |
P1 V+ |
Green/td>
| P2 V+ |
Red |
P1+ |
Orange |
P1+ |
Black |
P2+ |
Black |
P2+ |
Orange |
P1- |
Yellow |
P1- |
Brown |
P2- |
Brown |
P2- |
Yellow |
Having shuffled the pins around in the connector I ran both motors on my prototype driver board. After a short period of continuous
stepping the motors start to get quite quite hot so I think I will need to implement some form of PWM to keep the motors 'locked'
in position without dissipating too much power.